You can’t stay around in the titanium fabrication business for nearly half a century without quality being one of your core competencies. At TiFab the average experience of our craftsmen is 18 years and it shows in the quality of product we put out on a daily basis.
Quality starts from the RFQ stage of a project and is embedded in our culture throughout the sales process, into engineering and design, and all the way through fabrication, inspection, and delivery. We start with “the end in mind” and work our way back through every aspect of design and testing to ensure each piece of equipment meets our internal standards in addition to exceeding our customer’s standards.
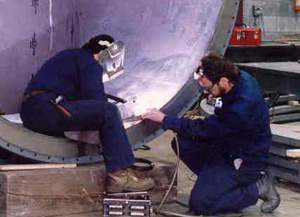

Both TiFab facilities have ASME Section VIII Div. 1 and 2, and R stamps, along with National Board Authorization for work in the industrial sector. For our Defense projects TiFab has approved Fabrication Plans per MIL-STD-278, and can weld to the highest standards for U.S. Navy and Army Applications. We have NAVSEA approval for welding all grades of titanium, up to six inches thick, per the NAVSEA Technical Publication S9074-AR-GIB 010-278.
On the testing side, our VT, PT, RT procedures are approved for most defense projects as well.
When sailor’s lives are on the line, the Navy chooses TiFab for their titanium and nickel alloy equipment that CANNOT fail. There is a reason they do.
Certifications
Defense
- NAVSEA Techpub 278
- NAVSEA Techpub 248
- NIST SP 800-171 Compliant
- ITAR Registration
ASME
- Section VIII Div 1 U-Stamp
- Section VIII Div 2 U-Stamp
- National Board Authorized